自動車製造工場1
75%の材料ロス削減と7.34トン/年間の
CO2排出量削減を達成しました
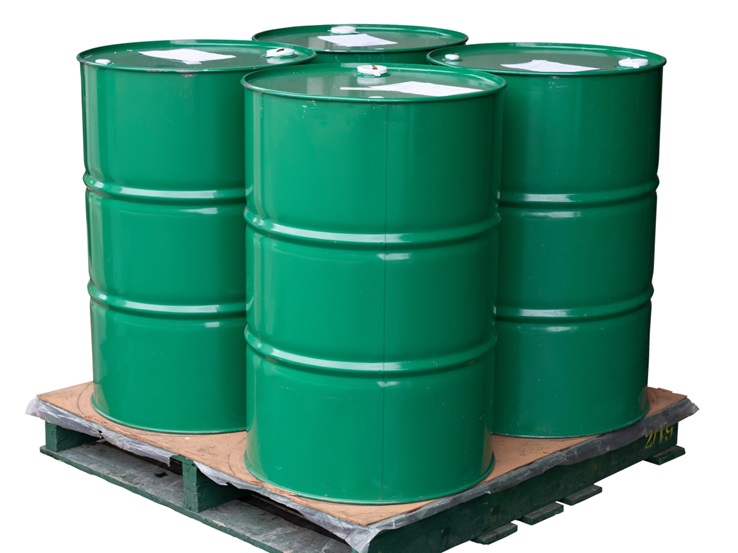
背景と課題について
導入背景と直面していた具体的課題
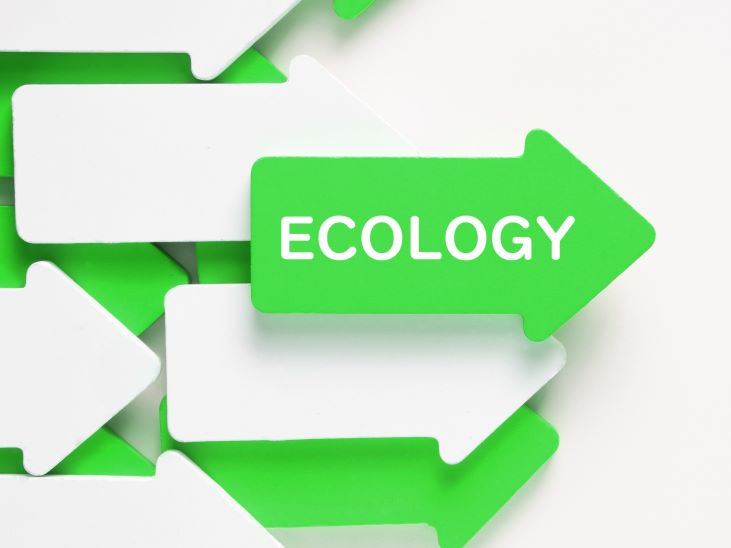
当工場ではドラム缶の交換作業時に大量のウレタン材がロスされる問題に直面していました。
このロスは、ドラム缶を交換する際に行われるエアパージ作業中に発生します。
エアパージとは、新しいドラム缶に切り替える際に、ポンプ内のウレタン材を抜く事によりエアーを押し出す作業です。
この作業で不必要に多くの材料が吐出されてしまい、それがコストの増加だけでなく、産業廃棄物の量を増やし、環境への負担も招いていました。
直面していた具体的な課題は以下の通りです。
第一に、エアパージ作業による材料コストとその使用による環境負担の増加。
第二に、エアパージ作業に伴う効率の低下、第三に、この過程で排出されるCO2の増加でした。
この問題に対応するためには、現行のエアパージ作業を改善し、材料の無駄を減らすとともに、環境への影響も考慮したシステムの導入が急務であったため、「パージレスシステム」を導入することにしました。このシステムの採用により、エアパージ作業によるウレタン材の廃棄量を大幅に削減し、材料の有効活用を図るとともに、CO2排出と廃棄物の問題にも解決を見込んでいます。
選定と導入
パージレスシステム導入によるコスト削減と環境保全
かねてより、ドラム缶交換時のエアパージ作業による材料ロスを問題視されていました。この問題に対処するため、
効率的な解決策として「パージレスシステム」の導入を検討し始めました。まず、この問題の詳細な分析を行い、様々な技術オプションを比較検討しました。
その中から、材料の無駄を最も削減できるシステムを選定するために複数の仕様にて、それぞれの性能とコストを評価しました。
評価の一環として実施されたパイロットテストでは、選出したシステムの効果を実際に検証し、その結果に基づいた調整を重ねました。テストの成功を受けコスト削減と環境負荷の低減の観点から、このシステムの全面的な導入を決定しました。導入後は、システムの運用状況を定期的にモニタリングし、さらなる改善点が発見されれば、迅速に対応を行っています。
この一連の選定と導入プロセスを通じて材料ロスを大幅に減らし、製造コストの削減及び環境への影響を低減するという目標を達成することができました。
成果と今後
パージレスシステム導入による成果と今後の展望
「パージレスシステム」は、ドラム缶交換時の材料ロスを大幅に削減することに成功しました。具体的には、従来8kgのウレタンが必要だったエアパージ作業が、2kgで済むようになり、1ドラム缶当たり6kgの材料を節約できるようになったのです。これにより、年間の原材料価格低減が実現しました。さらに、CO2排出量も年間で7.34トン削減することができ、環境保護にも寄与しています。
このシステムの導入は、単にコスト削減と環境への影響低減に留まらず、作業プロセスの効率化も図ることができました。具体的には、ドラム缶の交換時間が短縮され、清掃作業も容易になりました。
これにより、作業工数が改善、効率化されました。
今後の展望としては、このパージレスシステムのさらなる最適化を図り、他の製造ラインにも適用を広げていく計画です。また、技術的な進化を追求し、「完全パージレス」の実現を目指しています。これにより、更なるコスト削減と環境負荷の軽減を実現し、持続可能な生産活動を推進していくことが目標です。このような技術革新が、業界全体の標準を変え、より環境に優しい製造プロセスへと移行するきっかけになることを期待しています。